What Is Gearing Definition Hows Its Measured And Example
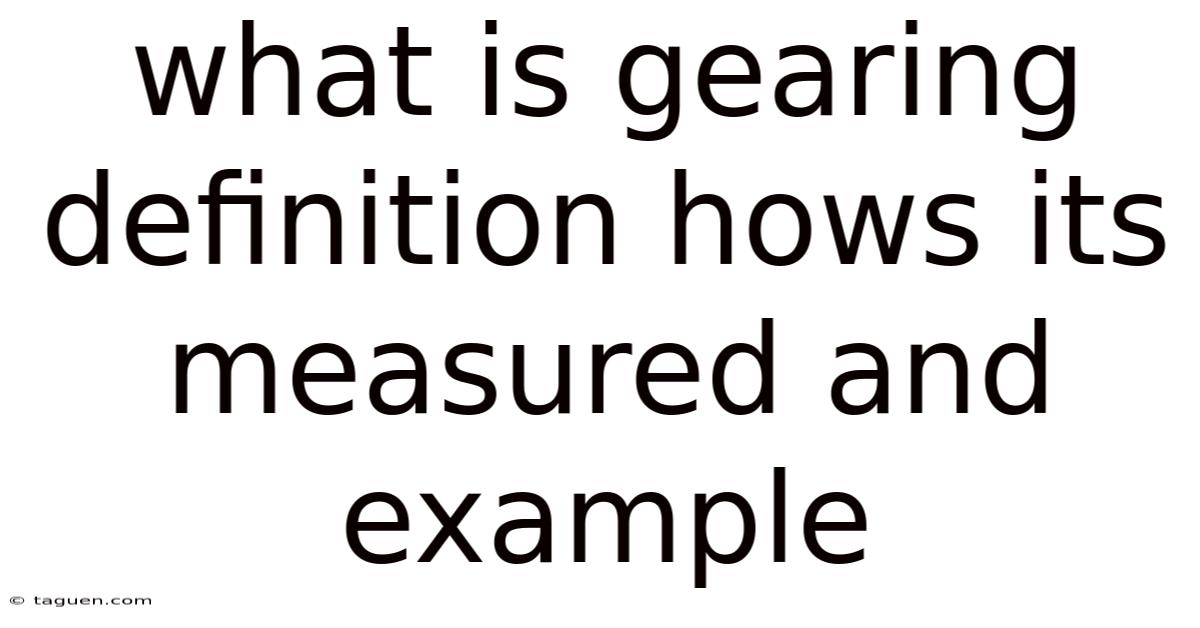
Discover more detailed and exciting information on our website. Click the link below to start your adventure: Visit Best Website meltwatermedia.ca. Don't miss out!
Table of Contents
Understanding Gearing: Definition, Measurement, and Real-World Examples
What exactly is gearing, and why does it matter in so many aspects of engineering and mechanics? This fundamental mechanical principle is the cornerstone of countless machines and systems, influencing efficiency, power transmission, and overall performance.
Editor’s Note: This article on gearing provides a comprehensive overview of the topic, covering its definition, measurement methods, and diverse applications with up-to-date examples.
Gearing, in its simplest form, refers to the mechanical advantage obtained through the use of gears. Gears are toothed wheels that mesh together to transmit rotational motion and torque from one shaft to another. This transmission can change the speed, torque, and direction of the rotation, providing a versatile tool for mechanical design. Understanding gearing is crucial across various engineering disciplines, from automotive engineering and robotics to manufacturing and power generation. The concept is fundamental to understanding how mechanical power is transferred and manipulated.
The Importance of Gearing and its Real-World Applications
The significance of gearing lies in its ability to efficiently transfer power while modifying its characteristics. This makes it indispensable in countless applications:
- Automotive Industry: Gearboxes in cars, trucks, and motorcycles use a system of gears to allow the engine to operate efficiently at different speeds and under varying loads. This enables smooth acceleration, efficient cruising, and the ability to handle steep inclines.
- Manufacturing and Robotics: Gearing is essential in numerous industrial machines, including conveyor belts, robotic arms, and automated assembly lines. It allows precise control of speed and torque, crucial for automating tasks and maintaining consistent production.
- Power Generation: Gear systems are used in wind turbines and hydroelectric power plants to step up or step down rotational speed, optimizing energy transfer and generator performance.
- Aerospace: Aircraft and spacecraft utilize gearing for various applications, such as controlling flight surfaces, operating landing gear, and managing propulsion systems.
- Consumer Products: Everyday devices like clocks, watches, and electric tools rely on gearing for precise movement and efficient power transfer.
This article delves into the core aspects of gearing, examining its definition, measurement techniques, various types, and real-world applications. Backed by examples and explanations, it aims to provide a comprehensive understanding of this vital mechanical principle.
Key Takeaways
This article will cover:
Key Aspect | Description |
---|---|
Definition of Gearing | A fundamental explanation of what gearing is and its basic principles. |
Gear Ratio Calculation | Methods for determining the gear ratio and its significance in power transmission. |
Types of Gears | An overview of different gear types and their applications. |
Measurement Techniques | How gear dimensions and performance are measured and analyzed. |
Real-World Examples | Case studies illustrating the practical applications of gearing in various fields. |
Challenges and Solutions | Potential issues in gear design and strategies for overcoming them. |
With a strong understanding of its fundamentals, let's explore gearing further, uncovering its applications, challenges, and future implications.
Definition and Core Concepts
Gearing involves the use of two or more interconnected gears to transmit rotary motion and torque. The fundamental principle relies on the interaction of teeth on the gears. When one gear rotates, its teeth engage with the teeth of the meshing gear, causing the second gear to rotate. The relationship between the rotational speeds and torques of the two gears is determined by the gear ratio.
A gear ratio is the ratio of the number of teeth on the driven gear (the gear receiving power) to the number of teeth on the driving gear (the gear transmitting power). A gear ratio of 2:1 means that for every two revolutions of the driving gear, the driven gear makes one revolution. This also implies a torque multiplication; the driven gear will have twice the torque of the driving gear. Conversely, a gear ratio of 1:2 would mean the driven gear spins twice as fast as the driving gear, but with half the torque.
Applications Across Industries
The applications of gearing are vast and varied. Here are some key examples:
- Automotive Transmission: A car's transmission uses a series of gears to match engine speed to wheel speed. Lower gears provide high torque for acceleration, while higher gears allow for higher speeds with lower engine RPMs.
- Bicycle Drivetrain: A bicycle's drivetrain employs gears to allow the cyclist to pedal at a comfortable cadence while maintaining appropriate speed on different terrains.
- Clockwork Mechanisms: Clocks and watches utilize intricate gear systems to precisely measure and display time. The gear ratios ensure accurate movement of the hands.
- Industrial Robots: Robots rely on gearing to achieve precise movements and control the torque applied to various parts during operation.
- Wind Turbines: Gearboxes in wind turbines step up the slow rotation of the turbine blades to a faster rotation suitable for generating electricity.
Challenges and Solutions
While gearing is highly efficient, certain challenges can arise:
- Wear and Tear: Gear teeth experience wear and tear due to friction and repeated engagement. This can lead to reduced efficiency and potential failure. Solutions include using high-quality materials, lubrication, and proper gear design.
- Backlash: Backlash refers to the small amount of play between meshing gear teeth. Excessive backlash can cause inaccuracies and vibrations. Precise manufacturing techniques and proper gear selection minimize this issue.
- Noise: Meshing gears can generate noise due to impact and friction. Careful design, precise manufacturing, and lubrication can reduce noise levels.
- Lubrication: Proper lubrication is critical for reducing wear and tear and ensuring smooth operation. The choice of lubricant depends on the operating conditions and gear materials.
Impact on Innovation
Gearing continues to be a vital component in many areas of technological advancement:
- Electric Vehicles: Electric vehicle transmissions use gearing to optimize efficiency and performance. The ability to precisely control torque is crucial for electric motors.
- Robotics: Advancements in robotics rely on sophisticated gear systems for precise and controlled movements. Miniaturization and improvements in gear design are enabling more complex robotic systems.
- Renewable Energy: Gearing plays a key role in harnessing renewable energy sources. Optimizing gear ratios is crucial for maximizing efficiency in wind and hydroelectric power generation.
Measuring Gear Parameters
Several parameters are crucial in characterizing a gear's performance and functionality:
-
Module (m): The module is a fundamental parameter defining the size of a gear. It's the ratio of the reference diameter (diameter of the pitch circle) to the number of teeth. It is expressed in millimeters (mm). A larger module indicates a larger gear.
-
Diametral Pitch (P<sub>d</sub>): In the imperial system, diametral pitch is used instead of module. It's the number of teeth per inch of pitch diameter.
-
Pressure Angle (Φ): This angle determines the shape of the gear teeth and affects the efficiency and load-carrying capacity of the gearset. Common pressure angles are 14.5° and 20°.
-
Circular Pitch (p): The distance measured along the pitch circle between corresponding points on adjacent teeth. It is related to the module by the formula: p = πm.
-
Addendum (a): The radial distance from the pitch circle to the top of a tooth.
-
Dedendum (b): The radial distance from the pitch circle to the bottom of a tooth.
-
Clearance (c): The radial distance between the top of a tooth on one gear and the bottom of a tooth on the meshing gear.
These parameters are measured using precision instruments like gear tooth verifiers and coordinate measuring machines (CMMs). The accuracy of these measurements is crucial for ensuring proper gear meshing and efficient power transmission.
Gear Ratio Calculation: A Detailed Look
Calculating the gear ratio is straightforward:
Gear Ratio = (Number of teeth on driven gear) / (Number of teeth on driving gear)
For example, if the driving gear has 20 teeth and the driven gear has 60 teeth, the gear ratio is 60/20 = 3:1. This means the driven gear rotates three times slower than the driving gear, but with three times the torque.
The gear ratio significantly impacts the speed and torque relationship between the input and output shafts. A higher gear ratio (greater than 1) results in increased torque but reduced speed, while a lower gear ratio (less than 1) results in increased speed but reduced torque.
Types of Gears
Various types of gears exist, each optimized for specific applications:
-
Spur Gears: These are the simplest type, with straight teeth parallel to the axis of rotation. They are suitable for low-speed, parallel-shaft applications.
-
Helical Gears: These gears have inclined teeth, providing smoother operation and higher load-carrying capacity compared to spur gears. They are commonly used in high-speed applications.
-
Bevel Gears: These gears are used to transmit power between shafts that intersect at an angle. They are frequently found in differential gearboxes in automobiles.
-
Worm Gears: These gears consist of a worm (screw-like gear) and a worm wheel. They provide a high gear ratio and self-locking capability.
-
Rack and Pinion Gears: These convert rotary motion into linear motion or vice-versa. They are commonly used in steering systems and linear actuators.
The choice of gear type depends on factors like speed, torque requirements, shaft arrangement, and space constraints.
Real-World Examples: Case Studies
Let's examine a few real-world applications in detail:
Case Study 1: Automotive Transmission
A typical car transmission uses a series of gear sets to achieve different gear ratios. First gear has a high gear ratio, providing high torque for acceleration. As the car speeds up, the driver shifts to higher gears, reducing the gear ratio for better fuel efficiency at higher speeds. The reverse gear utilizes an idler gear to reverse the direction of rotation.
Case Study 2: Wind Turbine Gearbox
Wind turbines have slow-rotating blades. To generate electricity efficiently, a gearbox steps up the rotational speed to the optimal range for the generator. This requires a high gear ratio, often achieved using planetary gear systems. These gearboxes are subjected to significant loads and require robust design and maintenance.
Case Study 3: Robotic Arm
Robotic arms use a combination of different gear types to achieve precise movements in multiple axes. This often involves using harmonic drives, which are compact and provide high gear ratios with low backlash.
Frequently Asked Questions (FAQ)
Q1: What is the difference between a gear ratio and a gear train?
A1: A gear ratio refers to the ratio between the number of teeth on two meshing gears. A gear train consists of multiple gears working together to transmit power.
Q2: How does lubrication affect gear performance?
A2: Lubrication reduces friction, wear, and noise, increasing efficiency and extending gear life.
Q3: What is backlash, and why is it important?
A3: Backlash is the play between meshing gear teeth. Excessive backlash can cause inaccuracies and vibrations.
Q4: What materials are commonly used for gears?
A4: Common materials include steel, cast iron, plastics, and non-metallic materials depending on the application's requirements.
Q5: How are gear dimensions determined?
A5: Gear dimensions are determined based on design requirements, including speed, torque, and load capacity, using standard gear design formulas and standards.
Q6: What are some common gear failures?
A6: Common gear failures include tooth breakage, wear, pitting, and scoring, often caused by excessive load, improper lubrication, or manufacturing defects.
Practical Tips for Maximizing the Benefits of Gearing
-
Choose the right gear type: Select the gear type best suited for the specific application, considering factors like speed, torque, and shaft arrangement.
-
Ensure proper lubrication: Use the correct lubricant and lubrication schedule to reduce wear and tear and ensure smooth operation.
-
Minimize backlash: Maintain minimal backlash to improve accuracy and reduce vibration.
-
Use high-quality materials: Choose strong and durable materials to extend gear life.
-
Proper gear alignment: Ensure proper alignment of gears to prevent premature wear and improve efficiency.
-
Regular inspection and maintenance: Regularly inspect gears for wear and tear and perform necessary maintenance to prevent failures.
-
Optimize gear ratio: Select the optimal gear ratio to achieve the desired speed and torque output.
-
Consider noise reduction techniques: Incorporate noise-reducing features in the gear design or use noise-damping materials.
Conclusion: The Enduring Relevance of Gearing
Gearing remains a fundamental aspect of mechanical engineering, impacting numerous industries and technological advancements. Understanding the principles of gearing, the various gear types, and the methods for calculating gear ratios is essential for engineers and designers. By addressing the challenges and leveraging the opportunities presented by gearing technology, we can continue to develop efficient and innovative mechanical systems. The future of mechanical design is inextricably linked to the ongoing refinement and application of this crucial mechanical principle.
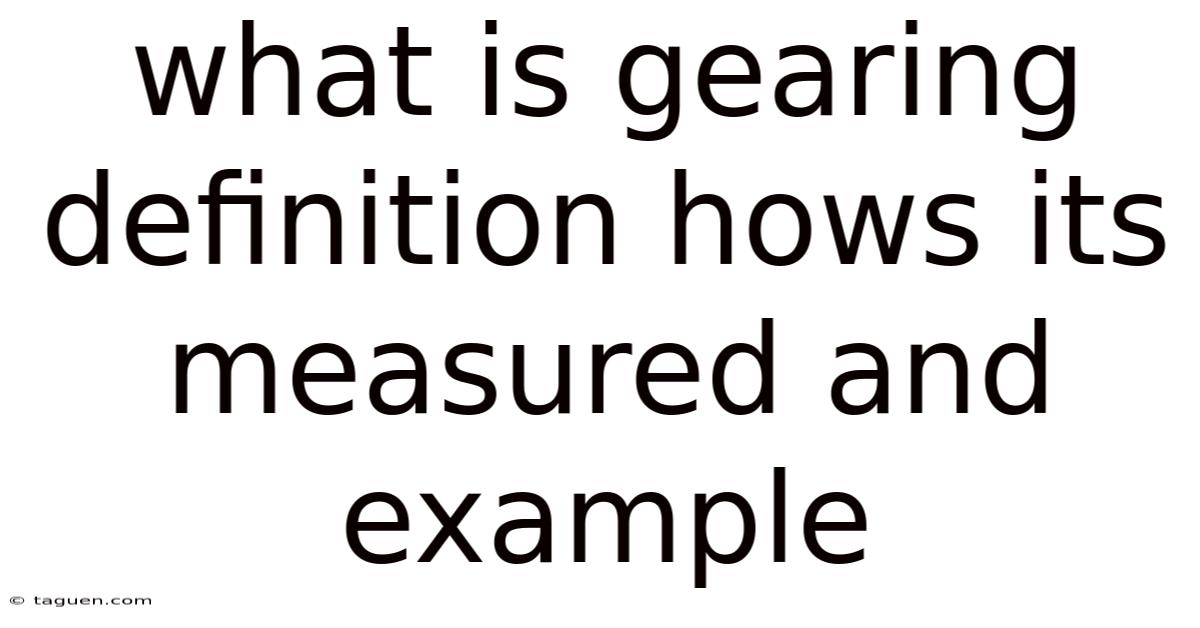
Thank you for visiting our website wich cover about What Is Gearing Definition Hows Its Measured And Example. We hope the information provided has been useful to you. Feel free to contact us if you have any questions or need further assistance. See you next time and dont miss to bookmark.
Also read the following articles
Article Title | Date |
---|---|
Group Of Five G5 Definition Current Countries Importance | Apr 18, 2025 |
Hindenburg Omen Definition 4 Main Criteria And Example | Apr 18, 2025 |
Historical Volatility Hv Definition Calculation Methods Uses | Apr 18, 2025 |
Hamburg Stock Exchange Ham Definition | Apr 18, 2025 |
Futures In Stock Market Definition Example And How To Trade | Apr 18, 2025 |