What Are Holding Costs Definition How They Work And Example
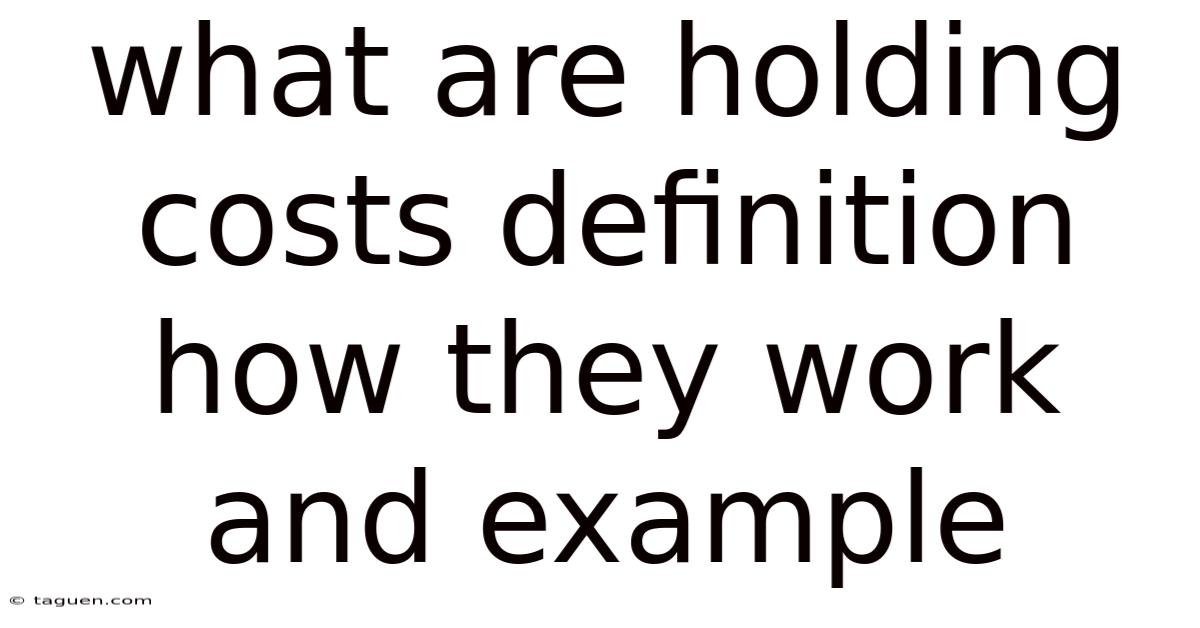
Discover more detailed and exciting information on our website. Click the link below to start your adventure: Visit Best Website meltwatermedia.ca. Don't miss out!
Table of Contents
Unveiling the Hidden Costs: A Deep Dive into Holding Costs
What if maximizing profitability hinges on understanding the often-overlooked burden of holding costs? These hidden expenses significantly impact your bottom line, and mastering their management is key to thriving in any competitive landscape.
Editor’s Note: This comprehensive guide to holding costs was published today, offering the most up-to-date insights and practical strategies for effective cost management.
Holding costs, also known as carrying costs or inventory holding costs, represent the total cost of storing and maintaining inventory. These expenses are far-reaching, impacting businesses of all sizes across various industries. Understanding and minimizing these costs is paramount for optimizing profitability and ensuring a healthy financial position. From warehousing expenses to insurance premiums, the components of holding costs are diverse and often underestimated. This article will demystify holding costs, providing a detailed explanation of their components, how they work, and practical strategies for effective management.
Key Takeaways: This article will delve into the core components of holding costs, explore their real-world applications across various industries, analyze the challenges in accurate calculation, and present actionable strategies for minimizing these often-overlooked expenses. Backed by examples and expert insights, this guide provides valuable knowledge for businesses seeking to enhance their financial performance.
The Depth of Our Research: This article is the culmination of extensive research, incorporating insights from leading supply chain experts, data from industry reports, and analysis of real-world case studies to ensure accuracy and reliability.
Key Holding Cost Component | Description | Example |
---|---|---|
Storage Costs | Rent, utilities, and maintenance of warehouse space. | Monthly warehouse rental fees, electricity bills |
Insurance Costs | Premiums to protect inventory against damage or loss. | Annual insurance policy for stored goods |
Taxes | Property taxes on inventory and warehouse facilities. | Annual property tax assessment |
Obsolescence Costs | Losses due to outdated or unsaleable inventory. | Value of obsolete electronics in a warehouse |
Spoilage and Deterioration Costs | Losses due to damage, decay, or expiration of perishable goods. | Spoiled food products in a grocery warehouse |
Pilferage and Shrinkage Costs | Losses due to theft or internal discrepancies in inventory counts. | Missing items due to employee theft |
Capital Costs (Opportunity Cost) | Return that could have been earned by investing the capital tied up in inventory. | Potential interest earned on invested funds |
Handling Costs | Costs associated with moving, sorting, and managing inventory within the warehouse. | Labor costs for warehouse workers |
Depreciation Costs | Loss in value of inventory due to aging or technological advancements. | Decrease in value of machinery over time |
Understanding the Mechanics of Holding Costs:
Holding costs are calculated as a percentage of the total inventory value. This percentage varies depending on the industry, the type of inventory, and the efficiency of the inventory management system. The formula often used is:
Holding Cost = (Storage Costs + Insurance Costs + Taxes + Obsolescence Costs + Spoilage/Deterioration Costs + Pilferage/Shrinkage Costs + Capital Costs + Handling Costs + Depreciation Costs) / Total Inventory Value
This formula, while seemingly straightforward, highlights the complexity involved in accurately determining holding costs. Each component requires careful consideration and accurate data collection. For example, accurately estimating obsolescence costs requires forecasting future demand and assessing the risk of products becoming outdated.
Let’s explore the core aspects of holding costs further, uncovering their applications, challenges, and future implications.
Definition and Core Concepts:
Holding costs encompass all expenses associated with storing and maintaining inventory until it is sold. It's crucial to understand that these are not merely physical storage expenses; they include the opportunity cost of capital tied up in inventory, the risk of obsolescence, and potential losses from damage or theft. Accurate calculation requires a comprehensive approach, considering all relevant factors.
Applications Across Industries:
The impact of holding costs is universal, though the specific components and their relative importance vary significantly across industries.
- Retail: Retailers face substantial holding costs due to high inventory turnover and the risk of seasonal obsolescence. Managing these costs effectively is critical to maintaining profit margins.
- Manufacturing: Manufacturers hold raw materials, work-in-progress, and finished goods, each incurring different holding costs. Efficient inventory management techniques are crucial to reduce costs and optimize production.
- Pharmaceuticals: The pharmaceutical industry faces unique challenges, including stringent storage requirements for temperature-sensitive products and significant obsolescence risks due to short shelf lives and regulatory changes.
- Technology: The rapid pace of technological advancement significantly increases the risk of obsolescence in the technology sector. Effective forecasting and agile inventory management are essential to minimize these costs.
Challenges and Solutions:
Accurately calculating and managing holding costs presents several significant challenges:
- Data Accuracy: Inaccurate inventory data leads to incorrect estimations of holding costs. Implementing robust inventory management systems and regular stock audits are crucial.
- Forecasting Inaccuracies: Poor demand forecasting results in overstocking or understocking, both of which increase holding costs. Advanced forecasting techniques, such as machine learning, can enhance accuracy.
- Hidden Costs: Many holding cost components are easily overlooked, leading to underestimation. Regular cost analysis and a comprehensive understanding of all relevant expenses are necessary.
- External Factors: Unexpected events like natural disasters or supply chain disruptions can significantly impact holding costs. Risk management strategies and contingency planning are crucial to mitigate these impacts.
Solutions to these challenges often involve:
- Implementing efficient inventory management systems: Utilizing technologies such as RFID and barcode scanning improves inventory tracking and accuracy.
- Optimizing warehouse layout and operations: Efficient warehouse design and material handling practices reduce storage costs and handling time.
- Improving demand forecasting: Utilizing advanced forecasting techniques and regularly reviewing forecasts enhances accuracy and minimizes overstocking.
- Negotiating favorable terms with suppliers: Longer payment terms and flexible order quantities can reduce capital tied up in inventory.
- Implementing robust security measures: Strengthening security measures reduces losses due to theft and pilferage.
Impact on Innovation:
The pressure to reduce holding costs drives innovation in inventory management and supply chain technologies. This includes the development of:
- Advanced forecasting tools: Machine learning algorithms and AI-powered solutions improve forecasting accuracy and reduce overstocking.
- Automated warehouse systems: Robots and automated guided vehicles (AGVs) optimize warehouse operations, reduce labor costs, and enhance efficiency.
- Blockchain technology: Blockchain offers enhanced transparency and traceability in the supply chain, reducing inventory discrepancies and improving inventory management.
- Improved inventory visibility: Real-time inventory tracking and data analytics provide better insights into inventory levels and movement, enabling proactive cost management.
Exploring the Relationship Between Inventory Turnover and Holding Costs:
Inventory turnover is directly related to holding costs. A high inventory turnover rate indicates that inventory is sold quickly, reducing the time goods spend in storage and thereby minimizing holding costs. Conversely, a low inventory turnover rate leads to increased holding costs due to prolonged storage and increased risks of obsolescence and spoilage. Efficient inventory management practices aim to optimize inventory turnover while meeting customer demand.
Roles and Real-World Examples:
- Just-in-Time (JIT) inventory: JIT minimizes inventory levels by receiving materials only when needed, significantly reducing holding costs but increasing the risk of stockouts. Toyota's pioneering use of JIT is a classic example.
- Vendor-Managed Inventory (VMI): VMI entrusts suppliers with managing inventory levels, optimizing stock levels and reducing holding costs for both parties. Many large retailers employ VMI systems with their key suppliers.
- Warehouse Management Systems (WMS): WMS software optimizes warehouse operations, improving efficiency and reducing storage and handling costs. Many companies utilize WMS to track inventory, manage shipments, and improve warehouse productivity.
Risks and Mitigations:
- Stockouts: Minimizing inventory to reduce holding costs increases the risk of stockouts, leading to lost sales and customer dissatisfaction. Safety stock levels help mitigate this risk.
- Obsolescence: Rapid technological advancements or changes in consumer preferences can render inventory obsolete, resulting in significant losses. Careful demand forecasting and agile inventory management practices help minimize these risks.
- Damage and Spoilage: Improper storage conditions can lead to damage or spoilage, resulting in inventory losses. Proper warehouse facilities and appropriate handling procedures are essential.
Impact and Implications:
Effective holding cost management directly impacts a company's profitability and competitiveness. Reduced holding costs translate to higher profit margins, increased cash flow, and improved inventory turnover. This, in turn, leads to stronger financial performance and a more competitive position in the marketplace.
Further Analysis: Deep Dive into Obsolescence Costs
Obsolescence costs are a significant, often underestimated, component of holding costs. These costs arise when inventory becomes outdated or unsaleable due to technological advancements, changes in consumer preferences, or other factors. The impact of obsolescence costs can be devastating, particularly in industries with rapid technological change.
Factor Influencing Obsolescence | Impact | Mitigation Strategy |
---|---|---|
Rapid technological advancements | Increased risk of products becoming outdated quickly. | Invest in research and development to stay ahead of trends |
Changing consumer preferences | Products may lose appeal, leading to unsaleable inventory. | Focus on product differentiation and market research |
Seasonal products | Inventory may become unsaleable after the season ends. | Optimize inventory levels to match seasonal demand |
Short product life cycles | Products quickly become outdated, leading to high obsolescence costs. | Adopt agile manufacturing and flexible production methods |
Regulatory changes | Products may become illegal or non-compliant, leading to write-offs. | Stay informed about relevant regulations and standards |
Frequently Asked Questions (FAQs):
-
What is the average holding cost percentage? The average holding cost percentage varies considerably across industries, typically ranging from 15% to 30% of the inventory value. However, this is just an average; specific percentages depend greatly on individual factors.
-
How can I accurately calculate my holding costs? Accurate calculation requires meticulous data collection and careful consideration of all cost components. Utilize robust inventory management systems and conduct regular stock audits to achieve precision.
-
How can I reduce my holding costs? Implementing efficient inventory management practices, optimizing warehouse operations, improving demand forecasting, and negotiating favorable terms with suppliers are effective strategies.
-
What is the impact of obsolescence on holding costs? Obsolescence significantly increases holding costs, potentially leading to substantial financial losses. Mitigating obsolescence risk requires careful product planning and effective forecasting.
-
What role does technology play in managing holding costs? Technology plays a crucial role in optimizing inventory management, providing real-time inventory visibility, and improving demand forecasting accuracy.
-
How can I improve my inventory turnover rate to reduce holding costs? Improving demand forecasting, employing effective inventory management techniques, and optimizing warehouse operations can all significantly boost inventory turnover rates.
Practical Tips for Maximizing the Benefits of Effective Holding Cost Management:
- Implement a robust inventory management system: This provides real-time visibility into inventory levels, enabling proactive management.
- Optimize warehouse layout and processes: Efficient warehouse layout reduces storage costs and handling times.
- Improve demand forecasting: Employ sophisticated forecasting techniques and regularly review predictions.
- Negotiate favorable payment terms with suppliers: This reduces capital tied up in inventory.
- Regularly review and analyze holding costs: Identify areas for improvement and track progress.
- Implement robust security measures: Minimize losses from theft and pilferage.
- Invest in appropriate storage equipment and facilities: This prevents damage and spoilage.
- Consider implementing a Just-in-Time (JIT) or Vendor-Managed Inventory (VMI) system: These can significantly reduce holding costs but require careful planning and risk mitigation.
Conclusion:
Holding costs are an often-overlooked yet critical aspect of business operations. By thoroughly understanding their components, accurately calculating them, and proactively managing them, businesses can significantly enhance profitability, optimize resource allocation, and maintain a competitive edge. The journey towards effective holding cost management is a continuous process of refinement and adaptation, demanding consistent monitoring, analysis, and a commitment to optimizing every aspect of the inventory lifecycle. The future of efficient operations hinges on a complete understanding and mastery of these vital costs.
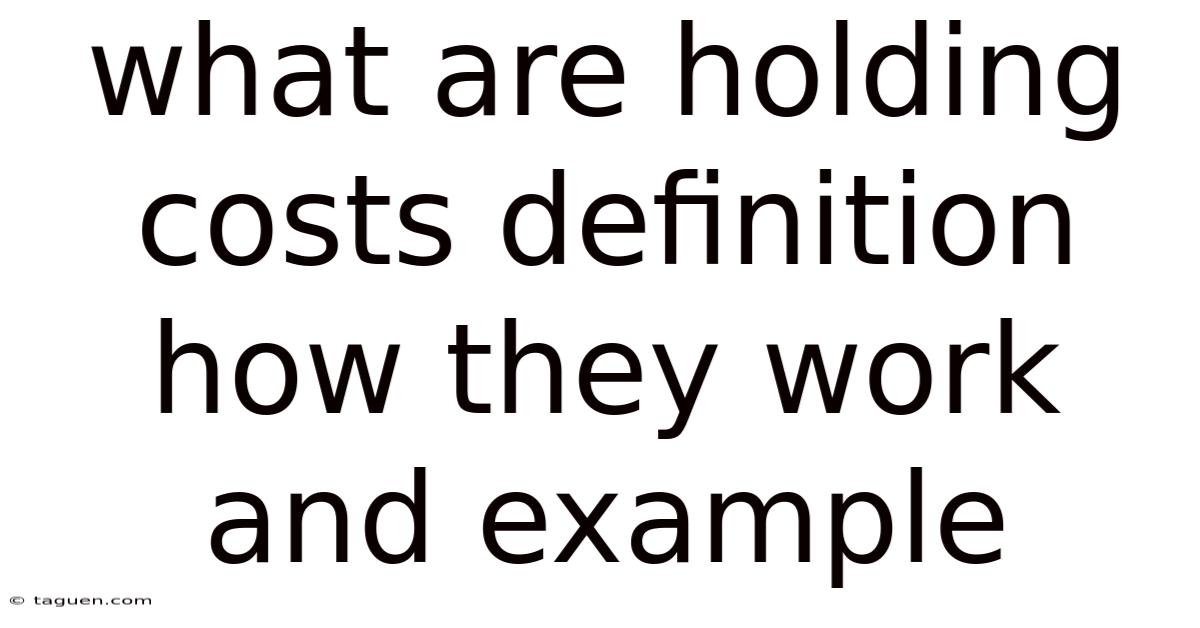
Thank you for visiting our website wich cover about What Are Holding Costs Definition How They Work And Example. We hope the information provided has been useful to you. Feel free to contact us if you have any questions or need further assistance. See you next time and dont miss to bookmark.
Also read the following articles
Article Title | Date |
---|---|
Growth At A Reasonable Price Garp Definition And Strategy | Apr 18, 2025 |
Gen Saki Definition | Apr 18, 2025 |
Gunslinger Definition | Apr 18, 2025 |
What Is Front Month Definition How It Works And Example | Apr 18, 2025 |
Herd Instinct Definition Stock Market Examples How To Avoid | Apr 18, 2025 |