Rig Utilization Rate Definition
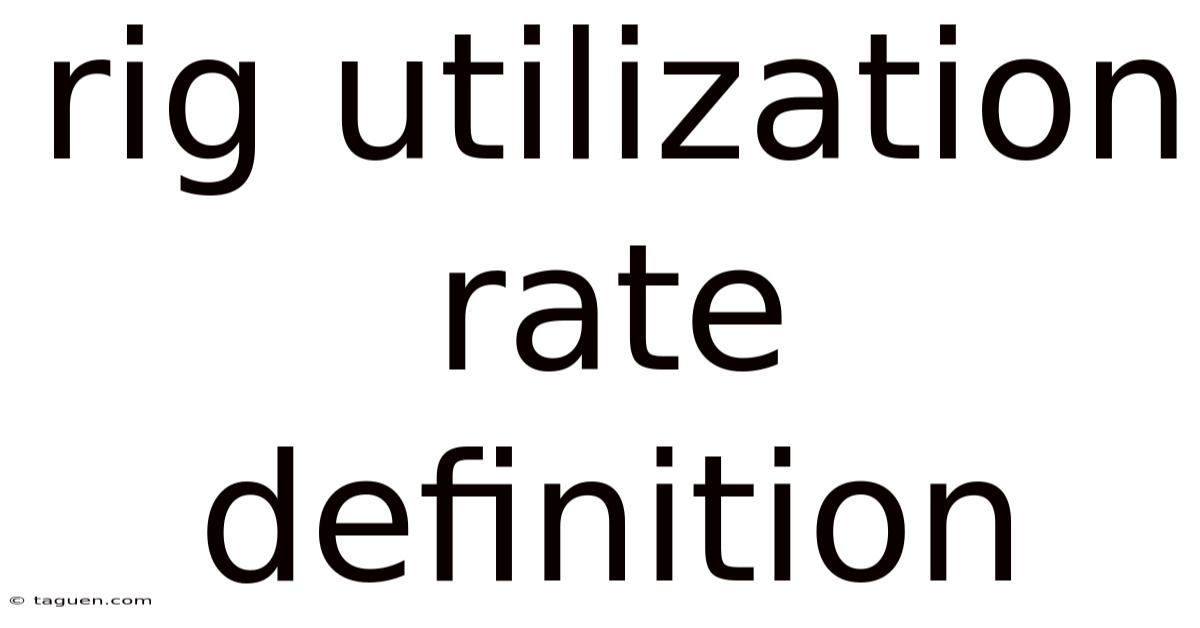
Discover more detailed and exciting information on our website. Click the link below to start your adventure: Visit Best Website meltwatermedia.ca. Don't miss out!
Table of Contents
Maximizing the Potential: A Deep Dive into Rig Utilization Rate Definition and Optimization
_What if maximizing your drilling rig's efficiency hinges on understanding a single metric? _ The rig utilization rate is not just a number; it's the key to unlocking significant cost savings and boosting overall profitability in the oil and gas industry.
Editor’s Note: This article on rig utilization rate definition and optimization has been published today, ensuring the latest insights and expert analysis for industry professionals.
Understanding rig utilization rate is essential for staying competitive in today's dynamic energy landscape. Its applications range from optimizing operational budgets to informing strategic investment decisions, impacting profitability and long-term success for drilling companies. This article delves into the core aspects of rig utilization rate, examining its definition, calculation methods, real-world applications, challenges, and future potential. Backed by expert insights and data-driven research, it provides actionable knowledge for industry professionals and enthusiasts alike. This comprehensive guide will explore its relationship with operational efficiency and offer practical strategies to improve this crucial metric.
This article explores the following key areas:
- Definition and Core Concepts: Defining rig utilization rate and its various interpretations.
- Calculation Methods: Different approaches to calculating the rate and their implications.
- Applications Across Industries: How the metric is used in onshore, offshore, and specialized drilling.
- Challenges and Solutions: Obstacles to high utilization rates and strategies for overcoming them.
- Impact on Innovation: How technology is driving improvements in rig utilization.
- The Relationship Between Downtime and Rig Utilization: Analyzing the impact of non-productive time.
- Further Analysis: Deep Dive into Downtime Classification: Categorizing and mitigating various downtime sources.
Key Takeaways:
Key Aspect | Description |
---|---|
Rig Utilization Rate | The percentage of time a drilling rig is actively engaged in productive operations. |
Calculation Methods | Vary depending on the included time periods (operational, calendar, etc.) and specific definitions of "productive time". |
Industry Applications | Crucial for cost management, operational planning, and investment decisions across all drilling sectors. |
Challenges & Solutions | Addressing equipment failures, permitting delays, weather disruptions, and workforce issues through preventative maintenance, planning, and improved communication. |
Impact of Downtime | Significant negative impact on overall utilization and profitability; requires detailed analysis and targeted mitigation strategies. |
With a strong understanding of its relevance, let’s explore rig utilization rate further, uncovering its applications, challenges, and future implications.
Definition and Core Concepts
Rig utilization rate, at its core, represents the proportion of time a drilling rig spends actively engaged in productive operations compared to the total available time. "Productive operations" can be defined differently depending on the company's specific needs and operational context. It typically includes drilling, well completion, and other directly revenue-generating activities. However, some companies may also include preparatory or ancillary tasks within the definition of productive time.
The total available time can be calculated based on a calendar year, a specific contract period, or a defined operational period. The choice of time frame significantly influences the calculated utilization rate. A calendar year approach provides a holistic view of annual performance, while a contract-based approach is useful for evaluating the efficiency of individual projects.
Calculation Methods
There are several methods for calculating rig utilization rate, each with its own advantages and disadvantages:
-
Calendar-Based Utilization: This method uses the total number of days in a year (or other defined period) as the denominator and the number of days the rig was productively engaged as the numerator. This provides a straightforward, easily understood measure. However, it might not accurately reflect operational realities, as it doesn't account for factors such as weather delays or planned maintenance.
-
Operational-Based Utilization: This method considers only the operational days within a defined period. This approach accounts for planned downtime, providing a more precise view of actual productive time. However, it requires careful tracking of operational vs. non-operational days.
-
Hours-Based Utilization: This approach utilizes hours instead of days, providing a more granular view of rig efficiency. This is particularly useful for rigs that operate around the clock and can highlight even minor periods of downtime.
The formula for calculating utilization rate, regardless of the method, typically follows this structure:
(Productive Time / Total Available Time) x 100% = Rig Utilization Rate
Applications Across Industries
The concept of rig utilization rate finds widespread application across various segments of the drilling industry:
-
Onshore Drilling: In onshore operations, utilization rates are heavily influenced by factors such as access to locations, permitting processes, and weather conditions. High utilization rates are crucial for maximizing returns on investment in expensive land-based drilling rigs.
-
Offshore Drilling: Offshore drilling operations face unique challenges, such as weather-related delays, logistical complexities, and stricter regulatory requirements. Efficient planning and risk mitigation are essential for achieving high utilization rates in this demanding environment.
-
Specialized Drilling: For specialized drilling techniques like directional drilling or horizontal drilling, utilization rates reflect the efficiency of advanced equipment and skilled personnel. Higher utilization directly correlates to faster well completion times and lower operational costs.
Challenges and Solutions
Achieving and maintaining high rig utilization rates faces several significant challenges:
-
Equipment Failures: Mechanical breakdowns and equipment malfunctions can lead to significant downtime. Regular maintenance programs and proactive monitoring are crucial for minimizing these disruptions.
-
Permitting Delays: Delays in obtaining necessary permits can significantly impact the operational schedule, reducing utilization. Proactive engagement with regulatory bodies and efficient permitting processes are essential.
-
Weather Disruptions: Unfavorable weather conditions, especially in offshore drilling, can halt operations for extended periods. Meticulous weather forecasting and contingency planning are crucial.
-
Workforce Issues: Lack of skilled personnel or labor disputes can result in delays and reduced productivity. Investing in training and fostering a positive work environment are vital for minimizing workforce-related challenges.
Impact on Innovation
Technological advancements are continuously driving improvements in rig utilization rates:
-
Predictive Maintenance: Utilizing sensor data and machine learning algorithms to predict equipment failures and schedule maintenance proactively, reducing unplanned downtime.
-
Automation and Robotics: Automating certain drilling tasks reduces human error and increases efficiency, thereby boosting utilization rates.
-
Digital Twins and Simulation: Creating virtual representations of drilling operations allows for optimization before actual implementation, minimizing risks and delays.
The Relationship Between Downtime and Rig Utilization
Downtime represents the period when a rig is not engaged in productive activities. It significantly impacts rig utilization, directly reducing the percentage of time spent on revenue-generating tasks. Understanding the causes of downtime is crucial for improving utilization rates.
Further Analysis: Deep Dive into Downtime Classification
Downtime can be categorized into several types:
- Mechanical Downtime: Caused by equipment failures or malfunctions.
- Operational Downtime: Caused by logistical issues, permitting delays, or other operational challenges.
- Weather Downtime: Caused by unfavorable weather conditions.
- Administrative Downtime: Caused by bureaucratic delays or administrative issues.
Analyzing each downtime category separately allows for targeted interventions and improvements.
Conclusion
Rig utilization rate serves as a critical performance indicator for drilling companies, reflecting operational efficiency and profitability. By addressing the challenges and leveraging technological advancements, companies can significantly improve their utilization rates, leading to cost savings, increased revenue, and a stronger competitive position in the dynamic oil and gas industry. The continuous pursuit of optimization, underpinned by data-driven analysis and proactive planning, is key to unlocking the full potential of drilling rigs.
Frequently Asked Questions (FAQs)
-
What is a good rig utilization rate? A generally accepted benchmark is above 80%, but this can vary depending on the specific operational context and industry segment.
-
How can I improve my rig utilization rate? Implementing proactive maintenance, optimizing logistics, and investing in technology are key strategies.
-
What are the major causes of low rig utilization? Equipment failures, weather delays, permitting issues, and workforce challenges are primary culprits.
-
How does rig utilization impact profitability? Higher utilization directly translates to increased revenue and reduced operational costs per well.
-
What role does data analysis play in improving utilization? Data analytics helps identify patterns in downtime, allowing for targeted improvements and proactive intervention.
-
How can technology help improve rig utilization? Predictive maintenance, automation, and digital twins offer significant potential for enhancing efficiency.
Practical Tips for Maximizing Rig Utilization
-
Implement a robust preventative maintenance program: Regular inspections and scheduled maintenance reduce unplanned downtime.
-
Optimize logistics and supply chain management: Ensure timely delivery of materials and equipment to minimize delays.
-
Invest in advanced technologies: Utilize predictive maintenance, automation, and digital twins to enhance operational efficiency.
-
Improve communication and collaboration: Foster strong communication between all stakeholders to address issues promptly.
-
Develop comprehensive contingency plans: Prepare for potential disruptions, such as weather delays or equipment failures.
-
Invest in workforce training and development: Ensure skilled personnel are available to operate and maintain equipment efficiently.
-
Utilize data analytics to identify and address recurring issues: Track downtime causes and implement targeted solutions.
-
Streamline permitting processes: Proactively engage with regulatory bodies to expedite approvals.
With its transformative potential, rig utilization rate is shaping the future of the drilling industry. By embracing its principles and addressing challenges, companies can unlock new opportunities for growth and innovation.
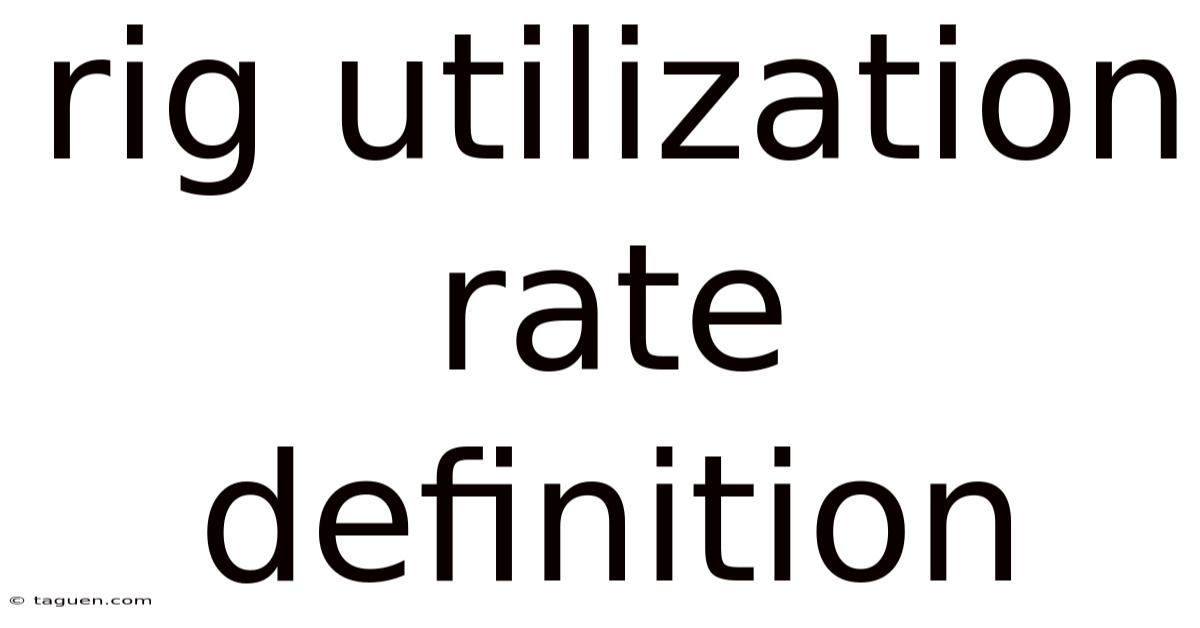
Thank you for visiting our website wich cover about Rig Utilization Rate Definition. We hope the information provided has been useful to you. Feel free to contact us if you have any questions or need further assistance. See you next time and dont miss to bookmark.
Also read the following articles
Article Title | Date |
---|---|
Risk Parity Definition Strategies Example | Apr 23, 2025 |
How To Get Back Into School With Defaulted Student Loans | Apr 23, 2025 |
Residential Mortgage Backed Security Definition Pros And Cons | Apr 23, 2025 |
Reserve Maintenance Period Definition | Apr 23, 2025 |
What Does It Mean To Take Profits In Stocks | Apr 23, 2025 |