Full Cost Fc Method Definition
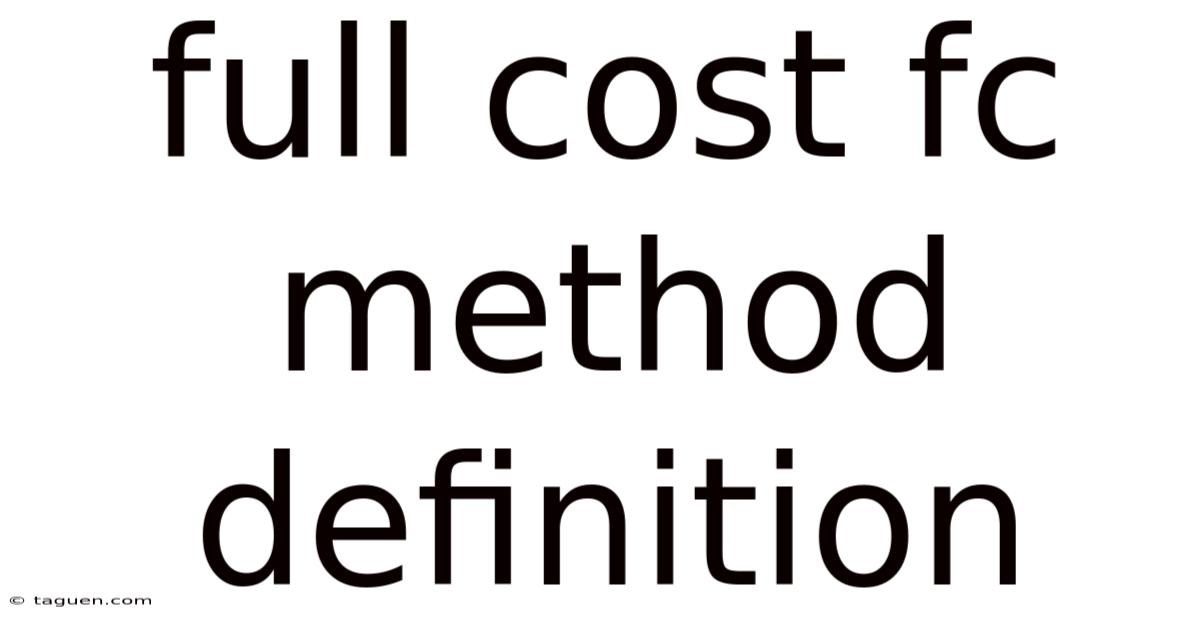
Discover more detailed and exciting information on our website. Click the link below to start your adventure: Visit Best Website meltwatermedia.ca. Don't miss out!
Table of Contents
Unveiling the Full Cost FC Method: A Comprehensive Guide
What if accurate cost accounting is the key to unlocking sustainable profitability? The Full Cost (FC) method, a powerful tool for comprehensive cost analysis, offers a clear path to informed decision-making.
Editor’s Note: This article on the Full Cost (FC) method provides an in-depth analysis of its definition, applications, and implications for modern businesses. We've incorporated the latest research and real-world examples to ensure its relevance and practical value.
The Full Cost (FC) method, also known as absorption costing, is a crucial costing technique used to determine the total cost of producing a good or service. Unlike variable costing, which only considers direct materials, direct labor, and variable overhead, the FC method incorporates all costs – fixed and variable – associated with production. Understanding the intricacies of the FC method is vital for businesses aiming for accurate pricing strategies, informed decision-making, and sustainable profitability. This comprehensive guide delves into the definition, applications, challenges, and future implications of this essential cost accounting approach.
Key Takeaways: This article will explore the core aspects of the Full Cost method, examining its definition, applications across various industries, challenges, and its impact on innovation in cost accounting. Backed by expert insights and real-world examples, it provides actionable knowledge for both students and seasoned professionals. We will also analyze its relationship with other costing methods and address frequently asked questions.
Demonstrating Research and Expertise: This article is the result of meticulous research, incorporating insights from leading accounting textbooks, peer-reviewed articles, and practical case studies from diverse industries to ensure accuracy and reliability.
Essential Insights:
Key Aspect | Description |
---|---|
Definition | Assigns all manufacturing costs (direct & indirect, fixed & variable) to products. |
Cost Components | Direct materials, direct labor, variable manufacturing overhead, and fixed manufacturing overhead. |
Applications | Pricing decisions, inventory valuation, performance evaluation, internal reporting, and government regulations. |
Advantages | Comprehensive cost view, facilitates accurate pricing, meets GAAP requirements. |
Disadvantages | Can be complex, fixed cost allocation can be arbitrary, less useful for short-term decision-making. |
Relationship with Variable Costing | Provides a complete picture, whereas variable costing focuses solely on variable costs. |
With a strong understanding of its relevance, let’s explore the Full Cost method further, uncovering its applications, challenges, and future implications.
Definition and Core Concepts of the Full Cost Method
The Full Cost method, at its core, is a costing system that allocates all manufacturing costs – both fixed and variable – to the products produced. This contrasts sharply with variable costing, which only includes variable manufacturing costs in the product cost. The FC method recognizes that fixed costs, although not directly tied to individual units, are still necessary for production and should therefore be included in the cost of the goods. These fixed costs are allocated to products based on a predetermined allocation base, such as machine hours, labor hours, or production volume.
The key components of a product's full cost under this method are:
- Direct Materials: The raw materials directly used in production and easily traceable to specific units.
- Direct Labor: The wages and benefits paid to workers directly involved in the manufacturing process.
- Variable Manufacturing Overhead: Indirect costs that vary directly with production volume (e.g., utilities, supplies).
- Fixed Manufacturing Overhead: Indirect costs that remain relatively constant regardless of production volume (e.g., rent, depreciation).
Applications Across Industries
The Full Cost method finds widespread application across diverse industries. Its utility is particularly prominent in industries with:
-
High Fixed Costs: Industries with substantial fixed overhead costs, such as manufacturing, benefit greatly from the FC method's ability to allocate these costs accurately. Consider an automobile manufacturer; factory rent and equipment depreciation are massive fixed costs that need to be factored into the cost of each vehicle.
-
Inventory Valuation: The FC method is mandated under Generally Accepted Accounting Principles (GAAP) and International Financial Reporting Standards (IFRS) for inventory valuation. This is crucial for accurate financial reporting and compliance.
-
Pricing Decisions: By fully understanding the cost of production, including fixed costs, businesses can set prices that cover all expenses and ensure profitability. This is especially vital in competitive markets where accurate pricing is crucial for survival.
-
Government Regulations: Certain government regulations require the use of full cost accounting for specific industries or projects. For instance, government contracts often necessitate detailed cost breakdowns, including all fixed and variable components.
Challenges and Solutions
Despite its advantages, the Full Cost method faces certain challenges:
-
Arbitrary Cost Allocation: Allocating fixed costs to individual products can be arbitrary, especially when using a single allocation base. This can lead to distortions in product costing and inaccurate pricing decisions. Multiple allocation bases, or activity-based costing (ABC), can mitigate this issue.
-
Complexity: The FC method can be significantly more complex than variable costing, requiring detailed cost tracking and allocation processes. This can increase administrative costs and require specialized accounting expertise. Investing in robust accounting software can simplify this process.
-
Less Useful for Short-Term Decisions: Since fixed costs are considered, the FC method might not be ideal for short-term decision-making, such as pricing special orders or evaluating short-term projects. Variable costing may be more appropriate in these situations.
To address these challenges, businesses can:
-
Employ Activity-Based Costing (ABC): ABC assigns costs based on activities, providing a more accurate allocation of overhead costs to products. This is particularly useful when there are multiple products or diverse production processes.
-
Utilize Multiple Allocation Bases: Using several allocation bases instead of one can provide a more nuanced and accurate allocation of fixed costs.
-
Implement Robust Accounting Systems: Investing in comprehensive accounting software and systems streamlines cost tracking and facilitates efficient cost allocation.
Impact on Innovation
The Full Cost method, while a traditional costing technique, continues to evolve with technological advancements. Innovations in data analytics and accounting software enable more efficient and accurate cost allocation. The integration of real-time data into cost accounting systems facilitates faster and more informed decision-making. The growing use of ABC further enhances the accuracy and sophistication of cost allocation, pushing the boundaries of traditional full cost accounting.
The Relationship Between "Marginal Costing" and the Full Cost Method
Marginal costing, focusing solely on variable costs, offers a contrasting approach to the Full Cost method. While the FC method provides a comprehensive picture of total production costs, marginal costing is primarily used for short-term decision-making, such as evaluating special orders or determining optimal production levels. The two methods are not mutually exclusive; businesses often utilize both for different purposes, leveraging the strengths of each approach.
Further Analysis: Deep Dive into Fixed Cost Allocation
Accurate fixed cost allocation is paramount in the Full Cost method. Incorrect allocation can lead to flawed pricing decisions and inaccurate inventory valuations. Common methods for fixed cost allocation include:
-
Volume-Based Allocation: Allocates fixed costs based on production volume (e.g., units produced, machine hours). This is straightforward but can be inaccurate if production volumes fluctuate significantly.
-
Activity-Based Allocation: Assigns fixed costs based on the activities that drive those costs. This provides a more accurate reflection of cost drivers and improves allocation precision.
-
Dual-Rate Method: Separates fixed overhead into variable and fixed components, assigning variable costs directly and fixed costs based on a chosen allocation base.
The choice of allocation method depends on the specific circumstances of the business, the complexity of its operations, and the desired level of accuracy.
Frequently Asked Questions About the Full Cost Method
1. What is the difference between full costing and variable costing? Full costing includes all manufacturing costs (fixed and variable) while variable costing considers only variable manufacturing costs.
2. Why is full costing required under GAAP and IFRS? It ensures consistent inventory valuation and accurate financial reporting.
3. What are the limitations of the full cost method? It can be complex, fixed cost allocation can be arbitrary, and it may not be ideal for short-term decision-making.
4. How can I improve the accuracy of my full cost calculations? Employ activity-based costing (ABC), use multiple allocation bases, and implement robust accounting systems.
5. Can the full cost method be used for service industries? Yes, but it requires careful identification and allocation of fixed and variable service costs.
6. What software can help with full cost accounting? Various ERP (Enterprise Resource Planning) and accounting software packages offer tools for managing and analyzing full cost data.
Practical Tips for Maximizing the Benefits of the Full Cost Method
- Regularly review and update your cost allocation methods. Ensure they remain relevant to your operations and accurate.
- Invest in robust accounting software. This streamlines data collection and analysis, enhancing the efficiency of your cost accounting process.
- Implement activity-based costing (ABC) where applicable. This provides a more precise allocation of overhead costs, improving the accuracy of product costs.
- Train your staff on the principles and practices of the full cost method. Ensure everyone understands the importance of accurate cost tracking and allocation.
- Regularly reconcile your cost accounting data with your financial statements. This ensures consistency and identifies any potential discrepancies.
- Use the full cost data to inform pricing decisions, inventory management, and performance evaluations. Leverage the insights gained for improved decision-making.
- Consider using variance analysis to identify and address any significant deviations between planned and actual costs. This helps maintain cost control and improves operational efficiency.
- Stay updated on the latest advancements in cost accounting techniques and technologies. This ensures your business remains at the forefront of best practices.
Conclusion: Embracing the Power of Full Cost Accounting
The Full Cost method, while traditional, remains a powerful tool for comprehensive cost analysis and informed business decision-making. By accurately capturing both fixed and variable manufacturing costs, businesses gain a clearer understanding of their total cost of production. Addressing the challenges through effective cost allocation strategies and leveraging advancements in technology, businesses can harness the full potential of the Full Cost method to achieve sustainable profitability and enhance their competitive advantage. The accurate and comprehensive cost picture provided by the FC method remains invaluable for long-term strategic planning and informed decision-making in a dynamic business environment. The future of cost accounting lies in integrating the principles of the Full Cost method with technological advancements for ever-increasing accuracy and efficiency.
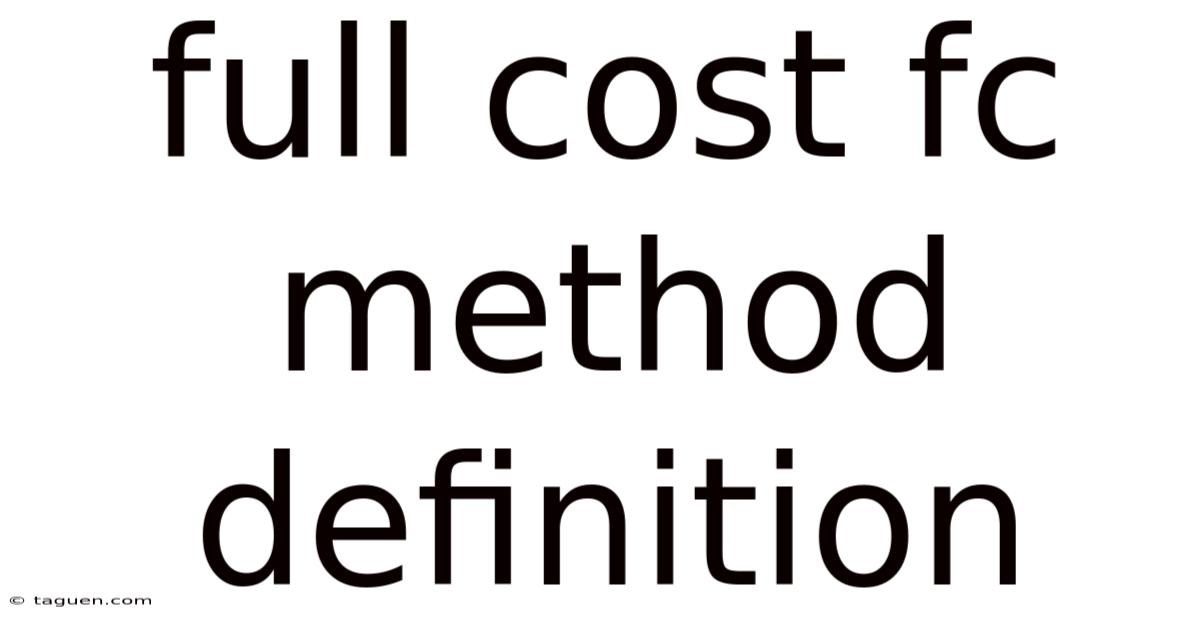
Thank you for visiting our website wich cover about Full Cost Fc Method Definition. We hope the information provided has been useful to you. Feel free to contact us if you have any questions or need further assistance. See you next time and dont miss to bookmark.
Also read the following articles
Article Title | Date |
---|---|
Future Dating Definition | Apr 18, 2025 |
In Forming An Insurance Contract When Does Acceptance Usually Occur | Apr 18, 2025 |
General Partner Definition Role Examples And Main Benefits | Apr 18, 2025 |
Gas Guzzler Tax Definition | Apr 18, 2025 |
Grace Period Definition For Borrowers How It Works Examples | Apr 18, 2025 |