Capacity Definition Business A Level
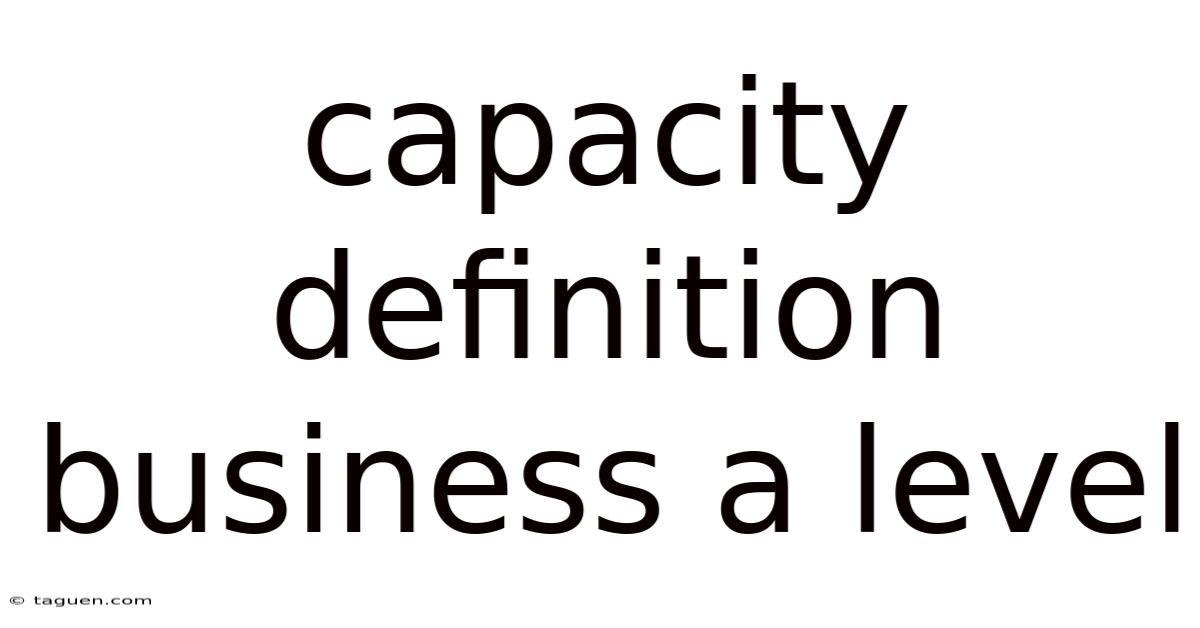
Discover more detailed and exciting information on our website. Click the link below to start your adventure: Visit Best Website meltwatermedia.ca. Don't miss out!
Table of Contents
Unlocking Business Success: A Deep Dive into Capacity Definition at A-Level
_What if the future of your business hinges on understanding capacity? _ Mastering capacity definition is the key to unlocking operational efficiency, strategic growth, and sustainable profitability.
Editor’s Note: This article on capacity definition in a business context has been thoroughly researched and updated to reflect current best practices and industry trends. It provides a comprehensive guide suitable for A-level business studies and beyond.
Understanding capacity is essential for any business aiming for sustained success. It's not just about possessing resources; it's about effectively utilizing those resources to meet demand and achieve strategic objectives. This article delves into the core aspects of capacity definition, examining its relevance, real-world applications, and future potential. Backed by expert insights and data-driven research, it provides actionable knowledge for aspiring business leaders and students alike.
This article explores the core aspects of capacity definition within a business context, examining its relevance, practical applications, and future implications. We will dissect the concept, explore its various dimensions, analyze its impact on different business functions, and offer practical strategies for maximizing its effective utilization.
Key Takeaways:
Key Aspect | Description | Importance |
---|---|---|
Capacity Definition | The maximum output a business can achieve within a given timeframe, considering resources and constraints. | Essential for planning, resource allocation, and strategic decision-making. |
Types of Capacity | Design capacity, effective capacity, actual output; understanding the differences is crucial for accurate assessment. | Accurate assessment allows for realistic planning and performance evaluation. |
Capacity Planning | Process of determining the appropriate level of capacity to meet future demand. | Prevents bottlenecks, ensures efficiency, and supports growth strategies. |
Capacity Constraints | Limitations on resources (e.g., labor, equipment, materials) affecting maximum output. | Identifying and mitigating constraints is crucial for optimizing capacity utilization. |
Capacity Measurement | Quantifying capacity using relevant metrics (e.g., units produced, customer served, machine hours). | Data-driven capacity analysis allows for informed decisions and performance improvements. |
Capacity Management Strategies | Techniques to adjust capacity (e.g., increasing workforce, investing in technology, outsourcing). | Enables businesses to adapt to fluctuating demand and maintain optimal performance. |
With a strong understanding of its relevance, let's explore capacity definition further, uncovering its applications, challenges, and future implications.
Defining Capacity: Core Concepts and Dimensions
Capacity, in a business context, refers to the maximum output a business can achieve within a specified timeframe. This output can be measured in various ways, depending on the nature of the business. For a manufacturing firm, capacity might be measured in units produced per hour, while for a service business, it could be the number of customers served per day. This definition incorporates both the potential and the limitations of a business.
Several key dimensions shape the understanding of capacity:
-
Design Capacity: This represents the maximum output a system could achieve under ideal conditions. It assumes perfect efficiency, no downtime, and readily available resources. It’s a theoretical maximum.
-
Effective Capacity: This is a more realistic measure, accounting for planned downtime, maintenance, and other factors that reduce the actual output achievable. It considers normal operational constraints.
-
Actual Output: This is the actual production achieved during a given period. It will always be less than or equal to the effective capacity. The difference between effective capacity and actual output highlights inefficiencies within the system.
Understanding the distinctions between these three types of capacity is critical for accurate assessment and planning. A business might have a high design capacity, but a lower effective capacity due to realistic constraints. Focusing solely on design capacity can lead to unrealistic expectations and poor planning.
Applications Across Industries
The concept of capacity has broad applications across various industries. Let's explore a few examples:
-
Manufacturing: Auto manufacturers carefully plan their production capacity to meet anticipated demand for new models. They consider factors such as available factory space, machinery, labor, and raw materials.
-
Healthcare: Hospitals manage their capacity by considering the number of beds, medical staff, and equipment available. Effective capacity planning is crucial for handling emergencies and ensuring optimal patient care.
-
Retail: Retailers must manage their shelf space, staffing levels, and inventory to meet customer demand. Understanding capacity is critical for managing peak seasons and preventing stockouts.
-
Tourism: Hotels and airlines must forecast demand to manage their capacity effectively. They utilize sophisticated forecasting models to predict peak seasons and adjust their pricing and service offerings accordingly.
-
Technology: Cloud service providers must manage their server capacity to handle fluctuating demand from users. They use sophisticated algorithms to scale their infrastructure and ensure service reliability.
Capacity Constraints: Identifying and Overcoming Bottlenecks
Capacity constraints represent limitations on resources that prevent a business from achieving its full potential. These constraints can be:
-
Financial: Insufficient capital to invest in new equipment or expand operations.
-
Human Resources: Lack of skilled labor or inadequate training.
-
Technological: Outdated machinery or inefficient processes.
-
Material: Shortages of raw materials or supply chain disruptions.
-
Space: Limited factory or office space.
Identifying and addressing these constraints is critical for optimizing capacity utilization. Techniques for overcoming bottlenecks include:
-
Investing in new technology: Automation can significantly improve efficiency and output.
-
Improving workforce skills: Training programs can enhance employee productivity.
-
Optimizing processes: Streamlining workflows can eliminate waste and improve efficiency.
-
Outsourcing: Delegating certain tasks to external providers can free up internal resources.
-
Expanding facilities: Increasing physical space can accommodate growing operations.
The Impact of Capacity on Innovation
Capacity planning is not merely an operational exercise; it significantly influences a company's ability to innovate. A business with sufficient capacity can allocate resources to research and development, leading to the creation of new products and services. Conversely, a business constrained by capacity might struggle to invest in innovation, potentially hindering long-term growth.
Capacity management also influences the speed of innovation. The ability to quickly scale operations in response to market demands allows businesses to capitalize on emerging opportunities and launch new products rapidly.
The Relationship Between Forecasting and Capacity
Accurate forecasting is crucial for effective capacity planning. Businesses must predict future demand to determine the appropriate level of capacity. This involves analyzing historical data, market trends, and other relevant factors. Forecasting errors can lead to overcapacity (resulting in wasted resources) or undercapacity (leading to lost sales and customer dissatisfaction). Sophisticated forecasting techniques, such as time series analysis and causal modeling, are often employed for improved accuracy. The accuracy of forecasting directly impacts the effectiveness of capacity planning. Inaccurate forecasts lead to either overinvestment or under-investment in capacity, both impacting profitability and competitiveness.
Capacity Management Strategies: Adapting to Change
Several strategies help businesses manage their capacity effectively:
-
Level Production: Maintaining a constant production rate despite fluctuations in demand. This requires careful inventory management.
-
Chase Demand: Adjusting production levels to match demand. This is more flexible but can be more costly.
-
Mixed Strategy: A combination of level production and chase demand, balancing flexibility and cost-efficiency.
-
Outsourcing: Using external providers to handle specific tasks or increase production capacity during peak times.
-
Lean Manufacturing: Focusing on eliminating waste and improving efficiency throughout the production process.
The choice of strategy depends on factors such as the nature of the product, demand variability, and cost considerations.
Exploring the Relationship Between Technology and Capacity
Technology plays a crucial role in shaping and enhancing capacity. Advancements in automation, information technology, and data analytics have revolutionized capacity management. These advancements allow for:
-
Increased efficiency: Automation reduces manual labor and improves productivity.
-
Improved forecasting: Data analytics provide more accurate demand predictions.
-
Better resource allocation: Sophisticated software optimizes resource utilization.
-
Enhanced flexibility: Cloud computing enables businesses to scale capacity up or down quickly.
-
Real-time monitoring: Real-time data monitoring allows for immediate adjustments to capacity levels.
The integration of technology is no longer optional but essential for businesses seeking to optimize capacity and maintain a competitive edge.
Frequently Asked Questions About Capacity Definition
-
What's the difference between capacity and capability? Capacity refers to the maximum output achievable, while capability refers to the potential to produce different goods or services. A business might have the capacity to produce 1000 units of Product A, but the capability to produce both Product A and Product B (perhaps at a lower total capacity).
-
How do I measure capacity effectively? Capacity measurement depends on the nature of the business. It could involve units produced, customer served, machine hours used, or other relevant metrics. Choose metrics that are relevant, measurable, and provide a clear picture of output.
-
What are the consequences of underestimating capacity? Underestimating capacity can lead to lost sales, dissatisfied customers, and missed business opportunities. It can also damage reputation and hinder growth.
-
How can I improve my capacity utilization? Improve efficiency through process optimization, employee training, technology upgrades, and waste reduction. Careful forecasting and effective resource allocation are also essential.
-
What are the risks of overestimating capacity? Overestimating capacity can lead to wasted resources (idle equipment, excess inventory), increased costs, and reduced profitability.
-
How can I plan for future capacity needs? Develop a long-term capacity plan based on forecasts, market analysis, and growth projections. Consider both short-term and long-term factors.
Practical Tips for Maximizing Capacity Benefits
-
Conduct regular capacity reviews: Assess your current capacity, identify bottlenecks, and develop strategies to improve efficiency.
-
Invest in employee training: A well-trained workforce is more productive and efficient.
-
Utilize technology effectively: Explore automation and data analytics tools to optimize capacity utilization.
-
Streamline processes: Eliminate unnecessary steps and improve workflows to reduce waste and improve efficiency.
-
Implement a robust forecasting system: Accurate demand forecasts are crucial for effective capacity planning.
-
Develop contingency plans: Prepare for unexpected events that might disrupt operations and impact capacity.
-
Embrace flexibility: Consider strategies that allow you to adapt to fluctuating demand.
-
Monitor key performance indicators (KPIs): Regularly track metrics that reflect capacity utilization and identify areas for improvement.
Conclusion: The Enduring Importance of Capacity in Business
Understanding and effectively managing capacity is fundamental to business success. By accurately assessing current capacity, anticipating future needs, and strategically managing resources, businesses can optimize their operations, drive innovation, and achieve sustained growth. Ignoring capacity planning risks missed opportunities, financial losses, and damage to reputation. The continuous optimization of capacity, informed by data, technology, and adaptable strategies, remains a cornerstone of building a thriving and resilient business. The dynamic nature of modern markets necessitates a continuous reassessment and refinement of capacity plans to remain competitive and responsive to evolving demands.
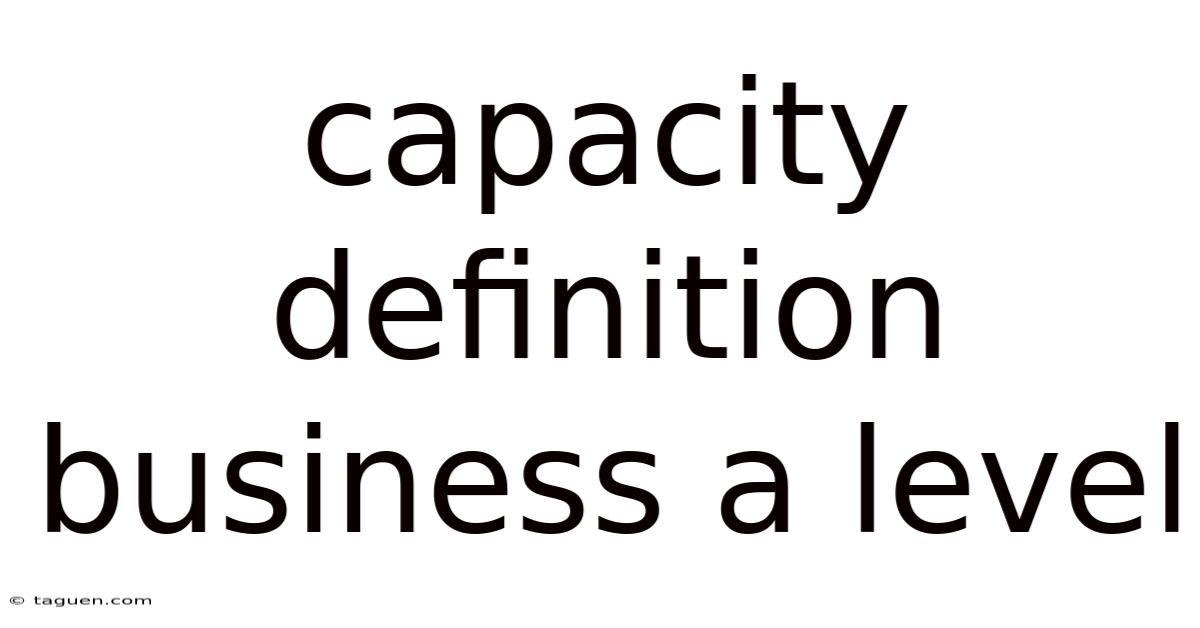
Thank you for visiting our website wich cover about Capacity Definition Business A Level. We hope the information provided has been useful to you. Feel free to contact us if you have any questions or need further assistance. See you next time and dont miss to bookmark.
Also read the following articles
Article Title | Date |
---|---|
Which Credit Bureau Wells Fargo Uses | Apr 09, 2025 |
3 Cs Of Credit Worthiness | Apr 09, 2025 |
Wells Fargo Credit Wise Card Reviews | Apr 09, 2025 |
Cost Of Dermatologist Visit Canada | Apr 09, 2025 |
Capital One Lower Interest Rate Reddit | Apr 09, 2025 |